At De-Yao Precision Company, we understand that quality is the cornerstone of a company’s survival and development. To ensure product quality, we regularly organize internal training sessions for our employees, introducing the goals and methods of 5S improvement. By disseminating concepts and practical exercises, we enable our quality control personnel to conduct quality control processes and inspections effectively.
1. Importance of Internal Training
Quality management is the core of our company’s operations. Through regular internal training, our quality control personnel can:
1. Update Professional Knowledge: Stay informed about the latest industry standards and technologies, ensuring inspection methods and equipment remain at the forefront.
2. Enhance Skill Levels: Improve practical operational capabilities through hands-on exercises, ensuring the accuracy of each inspection process.
3. Strengthen Quality Awareness: Instill a culture of quality first, helping every employee deeply understand the importance of quality.
2. 5S Improvement Goals and Methods
5S stands for Seiri (Sort), Seiton (Set in order), Seiso (Shine), Seiketsu (Standardize), and Shitsuke (Sustain). In our internal training, we emphasize the application of 5S to enhance the efficiency and quality of our work environment and processes.
1. Seiri (Sort): Remove unnecessary items to ensure a clean and orderly workplace.
2. Seiton (Set in order): Arrange work areas logically, allowing tools and materials to be organized for quick access.
3. Seiso (Shine): Maintain the cleanliness of equipment and work areas to prevent contamination and damage.
4. Seiketsu (Standardize): Develop and adhere to cleaning standards, ensuring a consistently clean work environment.
5. Shitsuke (Sustain): Cultivate good work habits and discipline among employees, continuously improving the effectiveness of 5S.
3. Training Content
Our internal training courses consist of both theoretical learning and practical operations:
1. Theoretical Learning: Covers fundamental principles of quality management, 5S management methods, and modern inspection technologies.
2. Practical Operations: Simulate actual production environments, allowing employees to practice and master inspection processes and techniques.
4. Continuous Improvement
Our internal training is not a one-time event but an ongoing process. Through regular training and continuous improvement, our quality control personnel maintain high levels of professional competence and operational skills, ensuring consistent enhancement of product quality.
De- Yao Precision will continue to emphasize quality management, consistently improving our employees’ professional skills to provide high-quality products and services to our customers. We believe that through continuous efforts, we will stand out in the competitive market, gaining more trust and support from our clients.
CNC Lathe Machining, CNC Machining Services, CNC Lathe Parts Manufacturing, High-Precision CNC Machining, Custom CNC Parts, CNC Metal Processing, Precision CNC Machining, CNC Lathe Manufacturing, Aluminum Alloy CNC Lathe Machining Services, Stainless Steel CNC Lathe Parts Manufacturing, CNC Lathe Machining Process, CNC Lathe Composite Machining, Rapid CNC Lathe Machining, Precision Parts, High-Precision CNC Lathe Machining Company, CNC Lathe Machining Technology Guide, Custom CNC Lathe Machining Services, Titanium Alloy CNC Precision Machining, CNC Milling and Turning Machining, Choosing a CNC Machining Factory, Die-Casting Process, Metal Die Casting, Aluminum Die Casting, Zinc Alloy Die Casting, Die Casting Factory, Casting Technology, Mold Design, Machining, Metal Processing, CNC Machining, Surface Treatment, Precision Machining, Die-Casting Parts, Machining Factory, Casting Alloys, Heat Treatment, Milling, Drilling, Grinding, Assembly Processing, Professional Design and Manufacturing Production Teamthe Machining Cost Evaluation, High Precision CNC Lathe Machining Company, CNC Lathe Machining Technical Guide, Custom CNC Lathe Machining Servic
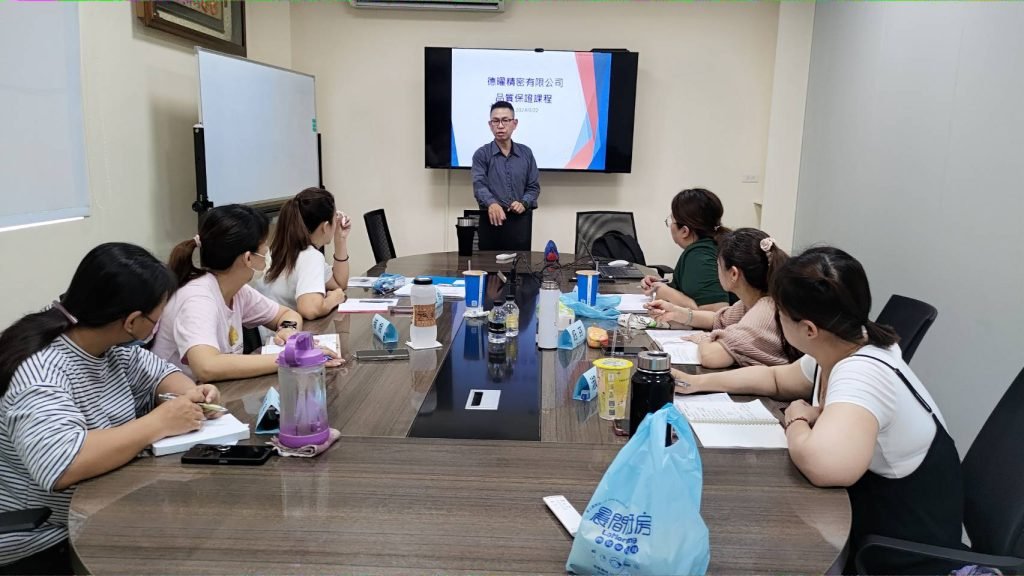
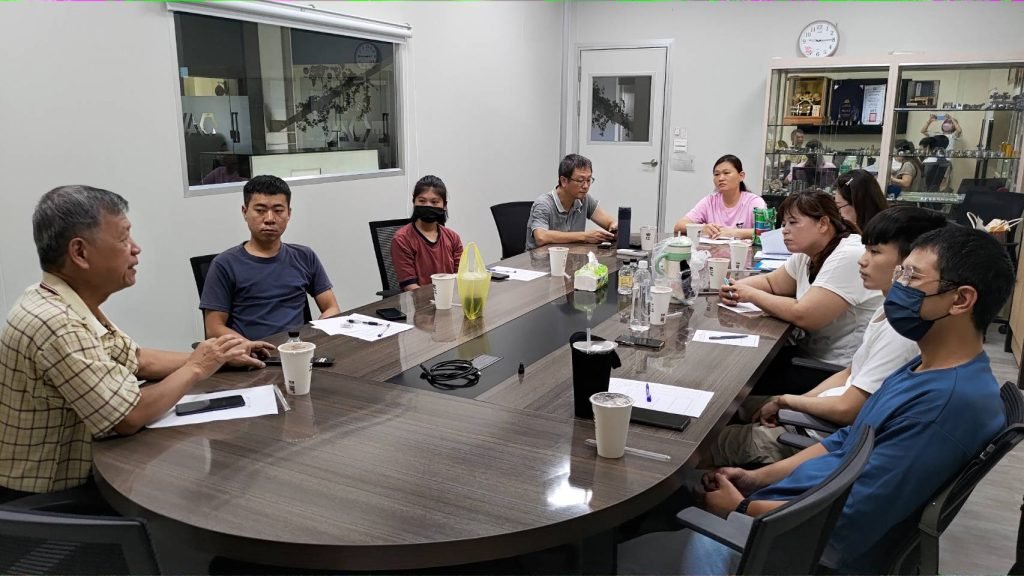